Understanding Smelting Plant Equipment: Essential Insights for Industrial Operations
Jul 05,2025
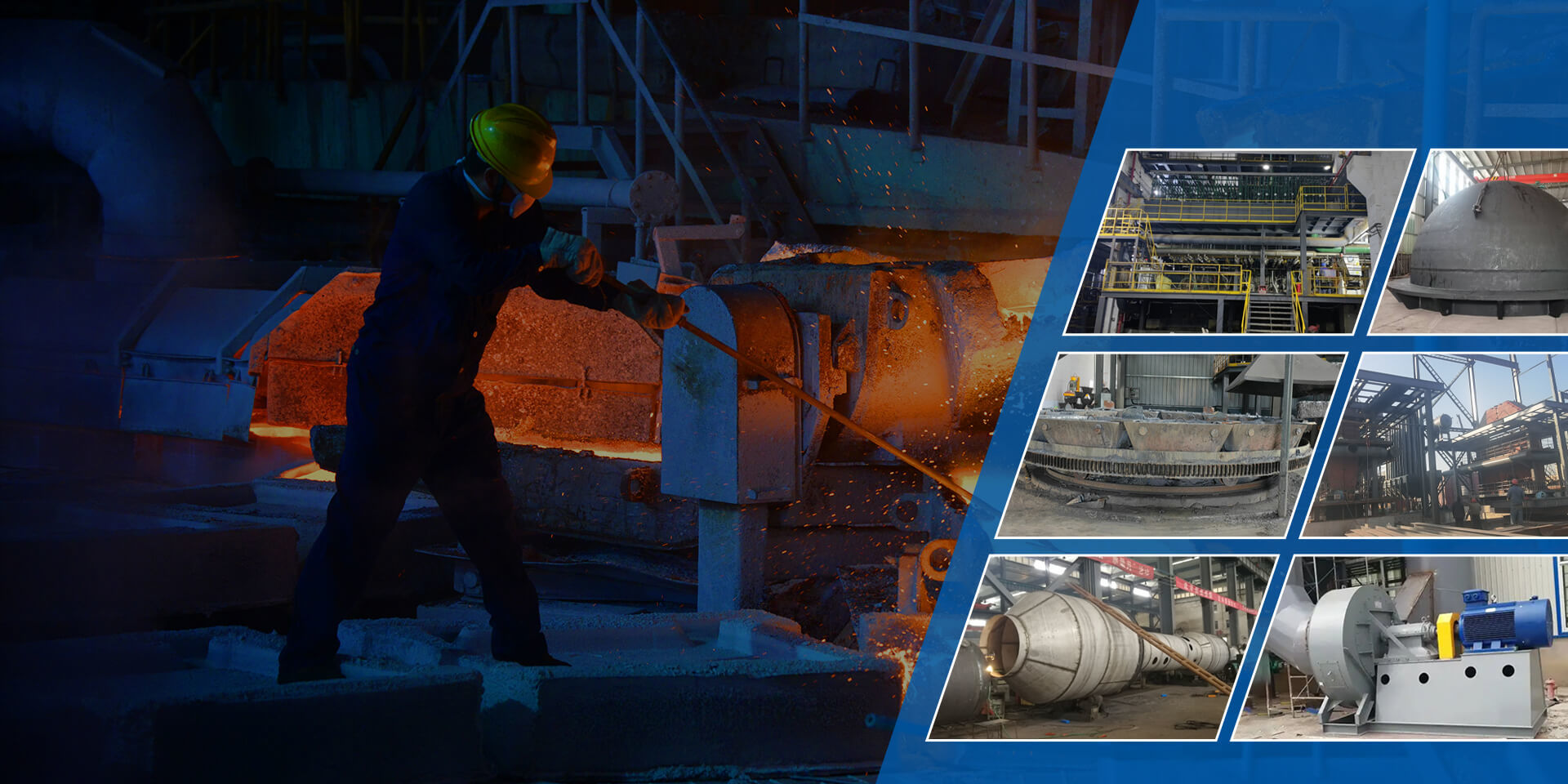
Smelting plant equipment plays a crucial role in the industrial sector, particularly in metallurgy and metal processing. This specialized equipment is designed for the extraction of metals from their ores through a combination of heating and chemical reduction processes. Understanding the different types of smelting equipment and their functions is essential for anyone involved in the field.
At the heart of any smelting operation are the furnaces, which are designed to reach extremely high temperatures necessary for melting ore. There are various types of furnaces used in smelting, including blast furnaces, electric arc furnaces, and induction furnaces. Each type has its unique advantages, depending on the specific metal being processed and the particular needs of the operation.
Blast furnaces are commonly used for iron and steel production. They operate by mixing iron ore, coke, and limestone, and then forcing hot air through the mixture. This process produces molten iron and slag, which can be further processed. Electric arc furnaces, on the other hand, are more flexible and can use scrap metal as their primary input. They utilize electric arcs to melt the metal, which allows for rapid temperature control and efficient energy use.
In addition to furnaces, smelting plant equipment includes various ancillary components such as slag handling systems, gas cleaning systems, and cooling systems. Slag handling systems are essential for managing the by-products of the smelting process, ensuring that waste is handled efficiently. Gas cleaning systems are vital for controlling emissions and ensuring environmental compliance, as smelting can produce harmful gases if not managed properly. Cooling systems are necessary to maintain the operational integrity of the equipment by preventing overheating.
The selection of appropriate smelting plant equipment is influenced by several factors, including the type of metal, the desired purity of the final product, and environmental regulations. Modern advancements in smelting technology enable processes that are not only more efficient but also more sustainable. Innovations such as automated monitoring systems and advanced materials for furnace linings have improved operational efficiency and reduced maintenance costs.
Training and safety measures are also critical when operating smelting equipment. Personnel must understand how to safely handle materials, manage equipment, and respond to emergencies. Adequate training helps reduce risks and ensures that operations run smoothly.
In conclusion, smelting plant equipment is a vital component of the industrial sector, facilitating the extraction and processing of metals. By understanding the different types of equipment and their functions, stakeholders can better appreciate how they contribute to efficient and effective operations in metallurgy. Whether in the selection of furnaces or the implementation of waste management systems, knowledge of smelting equipment is key to successful industrial practices.
At the heart of any smelting operation are the furnaces, which are designed to reach extremely high temperatures necessary for melting ore. There are various types of furnaces used in smelting, including blast furnaces, electric arc furnaces, and induction furnaces. Each type has its unique advantages, depending on the specific metal being processed and the particular needs of the operation.
Blast furnaces are commonly used for iron and steel production. They operate by mixing iron ore, coke, and limestone, and then forcing hot air through the mixture. This process produces molten iron and slag, which can be further processed. Electric arc furnaces, on the other hand, are more flexible and can use scrap metal as their primary input. They utilize electric arcs to melt the metal, which allows for rapid temperature control and efficient energy use.
In addition to furnaces, smelting plant equipment includes various ancillary components such as slag handling systems, gas cleaning systems, and cooling systems. Slag handling systems are essential for managing the by-products of the smelting process, ensuring that waste is handled efficiently. Gas cleaning systems are vital for controlling emissions and ensuring environmental compliance, as smelting can produce harmful gases if not managed properly. Cooling systems are necessary to maintain the operational integrity of the equipment by preventing overheating.
The selection of appropriate smelting plant equipment is influenced by several factors, including the type of metal, the desired purity of the final product, and environmental regulations. Modern advancements in smelting technology enable processes that are not only more efficient but also more sustainable. Innovations such as automated monitoring systems and advanced materials for furnace linings have improved operational efficiency and reduced maintenance costs.
Training and safety measures are also critical when operating smelting equipment. Personnel must understand how to safely handle materials, manage equipment, and respond to emergencies. Adequate training helps reduce risks and ensures that operations run smoothly.
In conclusion, smelting plant equipment is a vital component of the industrial sector, facilitating the extraction and processing of metals. By understanding the different types of equipment and their functions, stakeholders can better appreciate how they contribute to efficient and effective operations in metallurgy. Whether in the selection of furnaces or the implementation of waste management systems, knowledge of smelting equipment is key to successful industrial practices.
TAG:
Contact Us
Company Email:
962452762@qq.com
Contact Number:
+8615670922562
Company Address:
No. 11 Plant, Tiantan Industrial Park, Huling Industrial Cluster, Jiyuan City