Unlocking Efficiency: The Essential Guide to Choosing a Furnace for Metal Smelting
Jul 06,2025
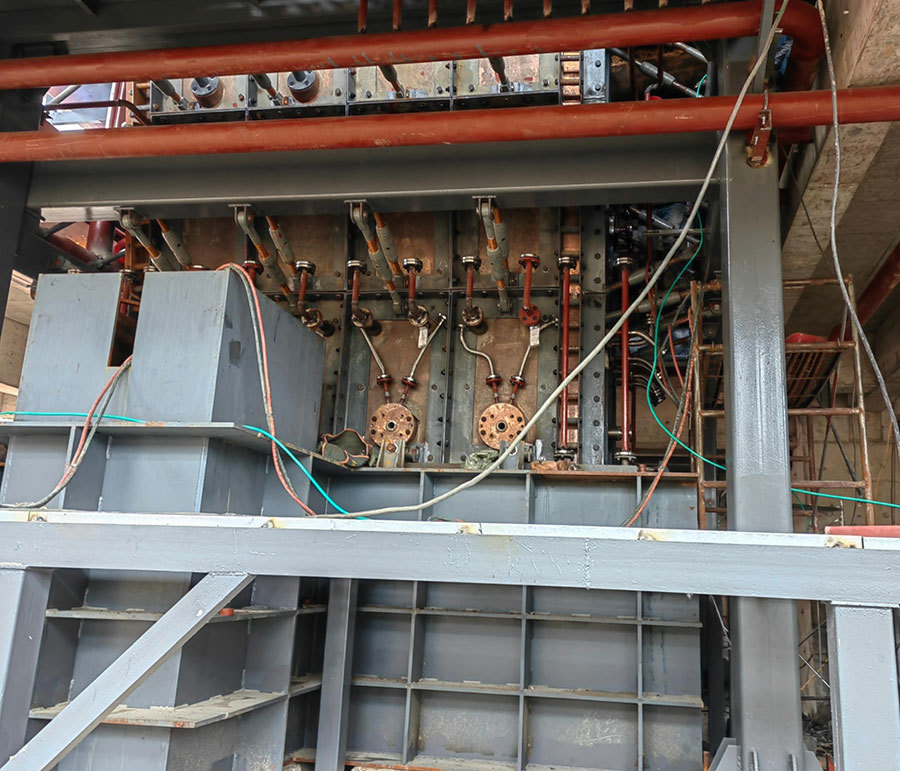
Unlocking Efficiency: The Essential Guide to Choosing a Furnace for Metal Smelting
Table of Contents
- 1. Introduction to Metal Smelting and Furnace Technologies
- 2. Importance of Choosing the Right Furnace for Metal Smelting
- 3. Common Types of Furnaces for Metal Smelting
- 4. Key Factors to Consider When Choosing a Furnace
- 4.1 Fuel Type and Energy Efficiency
- 4.2 Capacity and Size Requirements
- 4.3 Material Compatibility and Quality
- 4.4 Operational and Maintenance Costs
- 5. Technological Advancements in Furnace Design
- 6. Safety Considerations in Furnace Selection
- 7. Case Studies: Successful Furnace Implementations
- 8. Frequently Asked Questions
- 9. Conclusion
1. Introduction to Metal Smelting and Furnace Technologies
Metal smelting is a fundamental process in metallurgy, transforming raw ores into usable metals. The choice of furnace plays a pivotal role in this process, influencing both the quality of the end product and the overall efficiency of the operation. Understanding the various types of furnaces available, along with their operational nuances, is crucial for anyone engaged in metal smelting.
This guide aims to provide a detailed overview of the different furnace technologies, allowing businesses to make informed choices that enhance efficiency and productivity.
2. Importance of Choosing the Right Furnace for Metal Smelting
Choosing the right furnace is essential for several reasons:
- **Efficiency**: The right furnace can significantly reduce energy consumption, impacting overall operational costs.
- **Quality**: A furnace that suits specific smelting needs can lead to improved metal purity and better overall quality.
- **Adaptability**: Different processes might require specific types of furnaces, and having the right equipment enables flexibility in production.
Investing in the appropriate furnace technology can yield substantial long-term benefits, including reduced downtime and maintenance costs.
3. Common Types of Furnaces for Metal Smelting
Understanding the common types of furnaces used in metal smelting helps businesses make informed choices that align with their operational goals.
3.1 Induction Furnaces
Induction furnaces utilize electromagnetic induction to heat and melt metals. They are highly efficient, capable of achieving high temperatures quickly and with minimal energy loss. This type of furnace is particularly suitable for melting ferrous and non-ferrous metals, with applications ranging from small-scale operations to large foundries.
3.2 Arc Furnaces
Arc furnaces use an electric arc to generate heat, making them ideal for recycling scrap metal. They are known for their ability to melt a wide variety of metals, including steel and aluminum. The flexibility and efficiency of arc furnaces make them a popular choice in the steel manufacturing industry.
3.3 Blast Furnaces
Blast furnaces are traditionally used in the production of iron and steel. They operate by blowing hot air through layers of iron ore, coke, and limestone, resulting in molten iron. While they are not as energy-efficient as newer technologies, they remain a key component of large-scale operations.
3.4 Electric Furnaces
Electric furnaces, including resistance and induction types, are widely used for melting metals in precise and controlled environments. They offer excellent temperature control and are suitable for a range of applications, from small artisanal workshops to large industrial facilities.
4. Key Factors to Consider When Choosing a Furnace
When selecting a furnace for metal smelting, several critical factors should be evaluated to ensure optimal performance and efficiency.
4.1 Fuel Type and Energy Efficiency
Different furnaces operate on various fuel types, including natural gas, electricity, and oil. The choice of fuel impacts energy costs and efficiency. **Electric furnaces** are often considered more efficient, while **gas-powered furnaces** may offer lower operational costs depending on local energy prices.
4.2 Capacity and Size Requirements
The capacity of a furnace should match the scale of production. Businesses must analyze their production needs and choose a furnace size that offers the best balance between efficiency and throughput. Overly large furnaces can lead to wasted energy, while too-small furnaces may hinder production.
4.3 Material Compatibility and Quality
Not all furnaces are suitable for every metal type. It's important to choose a furnace compatible with the materials being processed, ensuring optimal melting and minimal contamination. This is especially crucial when working with high-grade materials or alloys.
4.4 Operational and Maintenance Costs
Understanding the long-term operational costs associated with running a furnace is vital. Factors such as maintenance requirements, downtime, and energy consumption can significantly affect overall expenses. It’s crucial to consider not just the initial investment but also the total cost of ownership over the furnace's lifespan.
5. Technological Advancements in Furnace Design
The field of furnace design is continually evolving, with advancements aimed at improving efficiency, safety, and environmental impact. Innovations such as **smart furnace technology** allow for real-time monitoring and automated adjustments, enhancing operational efficiency.
Additionally, the integration of **renewable energy sources** and advancements in heat recovery systems are gaining traction, further reducing the carbon footprint of metal smelting operations.
6. Safety Considerations in Furnace Selection
Safety should never be compromised in industrial operations. When choosing a furnace, businesses must consider safety features such as:
- **Emergency shutdown systems** to prevent accidents.
- **Ventilation** to counteract harmful fumes.
- **Temperature control mechanisms** to avoid overheating.
A comprehensive safety assessment should be part of the furnace selection process, ensuring compliance with industry regulations and standards.
7. Case Studies: Successful Furnace Implementations
Several companies have successfully implemented advanced furnace technologies to improve their metal smelting operations. One notable example is a large steel manufacturer that replaced traditional blast furnaces with induction furnaces. The result was a 30% reduction in energy consumption and an increase in production efficiency.
Another case involves an aluminum foundry that adopted electric arc furnaces to recycle scrap material. This transition not only lowered material costs but also enhanced environmental sustainability by reducing waste.
These examples illustrate the tangible benefits that can be achieved through careful furnace selection and implementation.
8. Frequently Asked Questions
What factors should I consider when choosing a furnace for metal smelting?
Consider fuel efficiency, capacity, material compatibility, operational costs, and safety features.
How do induction furnaces compare to electric arc furnaces?
Induction furnaces are highly efficient and suitable for various metals, while electric arc furnaces excel in recycling scrap metal and provide flexibility in operations.
What maintenance is required for metal smelting furnaces?
Regular inspections, cleaning of components, and monitoring of safety systems are essential for effective maintenance.
Can I use a single furnace for multiple types of metals?
It depends on the type of furnace and the specific metals. Some furnaces are versatile, while others are designed for specific materials.
What are the safety risks associated with metal smelting furnaces?
Potential risks include exposure to high temperatures, harmful fumes, and equipment malfunctions. Proper safety measures and equipment are essential to mitigate these risks.
9. Conclusion
Selecting the right furnace for metal smelting is a critical decision that impacts productivity, efficiency, and safety. By understanding the various types of furnaces available and considering key factors such as fuel type, capacity, and operational costs, businesses can make informed choices that align with their production needs.
Investing in modern furnace technologies and staying abreast of advancements in the field can lead to significant improvements in operational efficiency and sustainability. As the industry evolves, so too should the approaches to furnace selection and utilization, ensuring that businesses remain competitive in a rapidly changing market.
TAG:
Previous:
Contact Us
Company Email:
962452762@qq.com
Contact Number:
+8615670922562
Company Address:
No. 11 Plant, Tiantan Industrial Park, Huling Industrial Cluster, Jiyuan City