The Essential Guide to Smelting Furnace Equipment: Enhancing Efficiency in Metallurgical Processes
Jul 03,2025
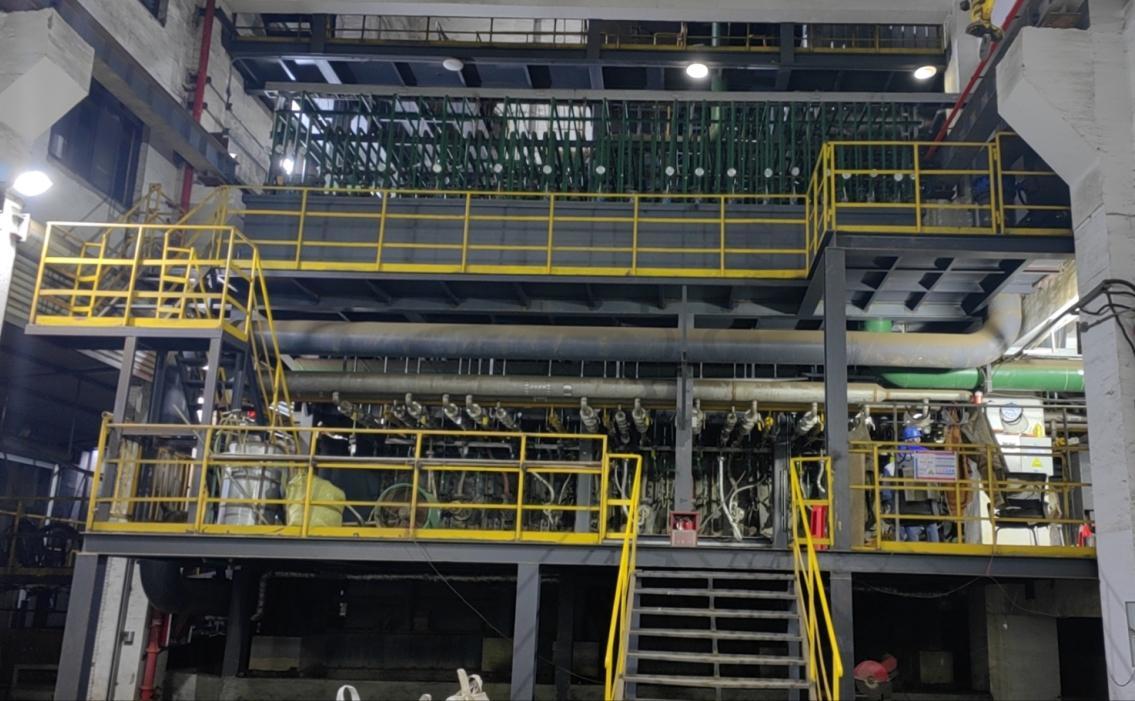
Smelting furnace equipment plays a pivotal role in the metallurgical industry, serving as the backbone for the extraction and processing of metals from their ores. As industries evolve, the demand for efficient and effective smelting solutions has increased, leading to advancements in technology and design. Understanding the various aspects of smelting furnaces can significantly enhance operational efficiency, reduce environmental impact, and improve overall productivity.
There are several types of smelting furnaces, each designed to cater to specific materials and processes. The most common types include electric arc furnaces (EAF), blast furnaces, and induction furnaces. Electric arc furnaces utilize electrical energy to melt scrap metal, making them ideal for recycling applications. Blast furnaces, traditionally used for iron and steel production, rely on chemical reactions between coke, iron ore, and limestone to produce molten iron. Induction furnaces, on the other hand, use electromagnetic fields to heat and melt metals, offering precise temperature control and reduced energy consumption.
Efficiency in smelting furnace equipment is influenced by various factors, including the choice of raw materials, furnace design, and operational parameters. Selecting high-quality raw materials can lead to improved smelting outcomes and reduced impurities in the final product. Moreover, advances in furnace design, such as improved insulation and heat recovery systems, can significantly lower energy costs and enhance the overall efficiency of the smelting process.
Another key consideration is the incorporation of automation and monitoring systems in smelting operations. Modern smelting furnaces are increasingly equipped with advanced sensors and control systems that allow for real-time monitoring of temperature, pressure, and chemical composition. This data-driven approach enables operators to make informed decisions, optimize process parameters, and minimize downtime.
Sustainability is also a pressing concern in the metallurgical industry. As regulations become stricter and the pressure to reduce carbon emissions heightens, smelting furnace equipment is evolving to meet these challenges. Innovations such as hybrid melting technologies and the use of alternative fuels are being explored to reduce the carbon footprint of smelting operations.
In conclusion, smelting furnace equipment is a critical component in the industrial landscape, driving the efficiency and effectiveness of metal production processes. By understanding the different types of furnaces, factors affecting efficiency, and the importance of sustainability, operators can make informed decisions that enhance their operations. Investing in advanced smelting technologies not only improves productivity but also contributes to a more sustainable future for the metallurgical industry.
There are several types of smelting furnaces, each designed to cater to specific materials and processes. The most common types include electric arc furnaces (EAF), blast furnaces, and induction furnaces. Electric arc furnaces utilize electrical energy to melt scrap metal, making them ideal for recycling applications. Blast furnaces, traditionally used for iron and steel production, rely on chemical reactions between coke, iron ore, and limestone to produce molten iron. Induction furnaces, on the other hand, use electromagnetic fields to heat and melt metals, offering precise temperature control and reduced energy consumption.
Efficiency in smelting furnace equipment is influenced by various factors, including the choice of raw materials, furnace design, and operational parameters. Selecting high-quality raw materials can lead to improved smelting outcomes and reduced impurities in the final product. Moreover, advances in furnace design, such as improved insulation and heat recovery systems, can significantly lower energy costs and enhance the overall efficiency of the smelting process.
Another key consideration is the incorporation of automation and monitoring systems in smelting operations. Modern smelting furnaces are increasingly equipped with advanced sensors and control systems that allow for real-time monitoring of temperature, pressure, and chemical composition. This data-driven approach enables operators to make informed decisions, optimize process parameters, and minimize downtime.
Sustainability is also a pressing concern in the metallurgical industry. As regulations become stricter and the pressure to reduce carbon emissions heightens, smelting furnace equipment is evolving to meet these challenges. Innovations such as hybrid melting technologies and the use of alternative fuels are being explored to reduce the carbon footprint of smelting operations.
In conclusion, smelting furnace equipment is a critical component in the industrial landscape, driving the efficiency and effectiveness of metal production processes. By understanding the different types of furnaces, factors affecting efficiency, and the importance of sustainability, operators can make informed decisions that enhance their operations. Investing in advanced smelting technologies not only improves productivity but also contributes to a more sustainable future for the metallurgical industry.
TAG:
Contact Us
Company Email:
962452762@qq.com
Contact Number:
+8615670922562
Company Address:
No. 11 Plant, Tiantan Industrial Park, Huling Industrial Cluster, Jiyuan City