Exploring the Benefits of Side-Blown Smelting Furnace Equipment: Unlocking Efficiency and Versatility
Jul 20,2025
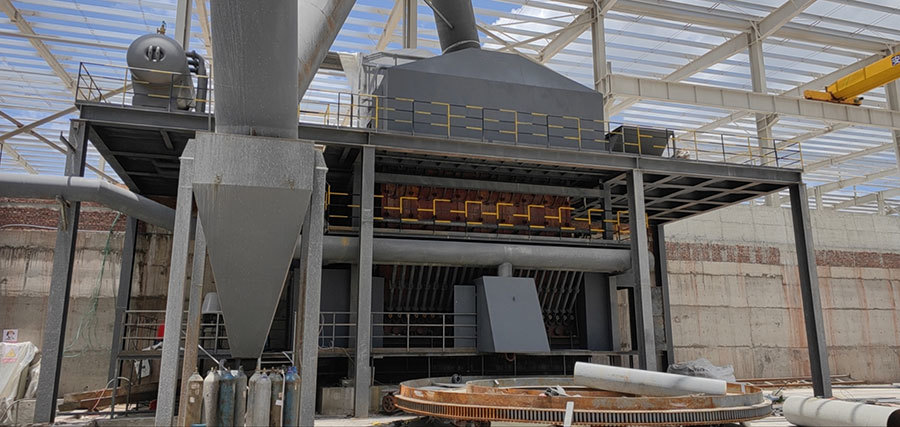
Exploring the Benefits of Side-Blown Smelting Furnace Equipment
Table of Contents
- Introduction to Side-Blown Smelting Furnaces
- How Side-Blown Smelting Furnaces Work
- Key Benefits of Side-Blown Smelting Furnace Equipment
- Applications of Side-Blown Smelting Furnaces
- Comparison with Other Smelting Technologies
- Environmental Impact and Sustainability
- Cost Analysis and Economic Advantages
- Future Trends in Smelting Furnace Technology
- Frequently Asked Questions
- Conclusion
Introduction to Side-Blown Smelting Furnaces
Side-blown smelting furnaces have emerged as pivotal equipment in the metallurgical industry, particularly for their unique ability to improve metal production processes. These furnaces utilize a distinct design that allows for the injection of air or oxygen from the side, facilitating effective smelting of various metals. As industries evolve and seek greater efficiency and sustainability, understanding the benefits of side-blown smelting furnace equipment becomes crucial.
In this article, we delve into the mechanics, advantages, and applications of side-blown smelting furnaces, providing a comprehensive overview of how they are transforming industrial practices.
How Side-Blown Smelting Furnaces Work
The operational principle of side-blown smelting furnaces is grounded in their innovative design. Unlike traditional top-blown furnaces, where air is introduced from above, side-blown furnaces allow for the injection of air or oxygen from the sides. This design enhances the distribution of airflow within the furnace, optimizing combustion and heat transfer.
The process typically begins with the charging of raw materials into the furnace. As these materials are heated, the injected air reacts with the fuel, generating intense heat. This heat facilitates the melting of metals, producing molten metal that can be tapped out at the bottom of the furnace. The controlled environment and efficient airflow significantly improve the refining process, resulting in higher yield and quality of the final product.
Key Benefits of Side-Blown Smelting Furnace Equipment
Enhanced Efficiency and Productivity
One of the primary advantages of side-blown smelting furnaces is their enhanced operational efficiency. The increased oxygen supply from the side injection allows for higher combustion rates, translating to faster melting times and improved throughput. As a result, industries can achieve higher production levels without compromising quality.
Improved Metal Quality
The side-blown design facilitates better mixing of materials, leading to a more homogeneous melt. This uniformity is crucial in achieving consistent metal quality, which is particularly important in applications where precision is paramount. Enhanced control over the melting process also minimizes the risk of defects, ensuring that the final product meets stringent industry standards.
Reduced Energy Consumption
Side-blown smelting furnaces operate more efficiently, often leading to reduced energy consumption. The optimized combustion process requires less fuel for the same level of output, resulting in significant cost savings over time. This energy efficiency is not only economically beneficial but also aligns with global sustainability goals.
Flexibility in Operation
The adaptability of side-blown smelting furnaces to various materials provides another compelling benefit. These furnaces can handle a range of feedstocks, including ferrous and non-ferrous metals, making them suitable for diverse industrial applications. This versatility enables manufacturers to respond swiftly to market demands and material availability.
Lower Emissions and Environmental Impact
With increasing scrutiny on industrial practices concerning environmental impacts, the lower emissions associated with side-blown smelting furnaces are noteworthy. The design promotes more complete combustion, resulting in fewer emissions of harmful gases. This feature makes side-blown furnaces a more environmentally friendly choice for metal production.
Applications of Side-Blown Smelting Furnaces
Side-blown smelting furnaces find applications across various sectors, each benefiting from their unique capabilities. Here are some prominent applications:
Steel Production
In the steelmaking industry, side-blown furnaces play a crucial role in scrap melting and alloy production. Their ability to produce high-quality steel with minimal impurities makes them an essential component of modern steel mills.
Non-Ferrous Metal Processing
These furnaces are widely used in the processing of non-ferrous metals, such as copper and lead. The side injection of air enhances the oxidation of impurities, leading to purer final products.
Foundries
Foundries benefit from the flexibility of side-blown furnaces in casting applications. The ability to melt various alloys and control the composition of molten metal makes them ideal for producing complex castings.
Recycling Facilities
The recycling industry utilizes side-blown smelting furnaces to efficiently process scrap metals, turning waste into valuable resources. Their energy efficiency and reduced emissions align well with sustainable practices in recycling.
Comparison with Other Smelting Technologies
When evaluating smelting technologies, it is essential to consider the distinct advantages that side-blown furnaces offer compared to other methods such as top-blown and electric arc furnaces.
Side-Blown vs. Top-Blown Furnaces
While both types of furnaces serve the same purpose, side-blown furnaces generally provide better control over the melting process. The side injection system allows for more effective heat distribution and reduces the risk of excessive oxidation, resulting in superior metal quality.
Side-Blown vs. Electric Arc Furnaces
Electric arc furnaces (EAF) are considered highly efficient for certain applications, particularly in metal recycling. However, side-blown furnaces can be more versatile in handling various feedstocks, making them a preferred choice for manufacturers with diverse production needs. Additionally, the initial capital investment for side-blown furnaces can often be lower than that of EAFs.
Environmental Impact and Sustainability
The environmental benefits of side-blown smelting furnaces cannot be overstated. As industries are increasingly held accountable for their carbon footprints, adopting technologies that promote sustainability is essential. Side-blown furnaces contribute to these goals through:
Lower CO2 Emissions
The efficient combustion process of side-blown furnaces leads to reduced carbon dioxide emissions compared to traditional smelting methods. This reduction is crucial in mitigating climate change and fulfilling regulatory compliance.
Resource Efficiency
By maximizing the recovery of materials from the melting process, side-blown furnaces enhance resource efficiency. This capability is particularly important in a world striving for circular economy practices where waste reduction is a priority.
Integration with Renewable Energy
The adaptability of side-blown furnaces allows them to be integrated with renewable energy sources, further reducing reliance on fossil fuels. This integration represents a significant step towards achieving energy sustainability in the metallurgical sector.
Cost Analysis and Economic Advantages
The economic benefits of using side-blown smelting furnaces extend beyond energy savings. A comprehensive cost analysis reveals several key factors:
Reduced Operating Costs
The efficiency of side-blown furnaces translates directly into lower operating costs. Reduced fuel consumption and higher output yield result in significant savings that can enhance a company's bottom line.
Lower Maintenance Costs
The design of side-blown furnaces often leads to lower maintenance requirements than other furnace types. With fewer moving parts and enhanced durability, facilities can minimize downtime and maintenance expenses.
Long-Term Investment
Investing in side-blown smelting furnace technology can prove beneficial in the long run. While initial costs may vary, the combination of operational efficiency, lower emissions, and adaptability ensures a strong return on investment as industries strive for modernization and sustainability.
Future Trends in Smelting Furnace Technology
As industries continue to innovate, the future of smelting furnace technology looks promising. Key trends to watch include:
Automation and Smart Technologies
The integration of automation and digital technologies is expected to enhance the efficiency of smelting processes further. Smart furnaces equipped with sensors can provide real-time data, allowing for better control and optimization.
Continued Focus on Sustainability
As environmental regulations tighten, the demand for sustainable smelting solutions will persist. The side-blown furnace’s inherent design advantages position it well in this evolving landscape, as industries seek to minimize their ecological impact.
Research and Development
Ongoing research will likely lead to further innovations in furnace design and operation, focusing on improving energy efficiency and reducing emissions even more. This commitment to advancement is essential for meeting future market demands and regulatory standards.
Frequently Asked Questions
1. What materials can be processed in side-blown smelting furnaces?
Side-blown smelting furnaces are versatile and can efficiently process a range of materials, including ferrous and non-ferrous metals such as copper, lead, and steel.
2. How do side-blown furnaces compare in cost to traditional smelting methods?
While initial costs can vary, side-blown furnaces generally offer lower operating costs over time due to their efficiency, energy savings, and reduced maintenance requirements.
3. Are side-blown smelting furnaces environmentally friendly?
Yes, side-blown furnaces produce lower emissions and utilize energy more efficiently, contributing to a reduced environmental impact and aligning with sustainability initiatives.
4. What industries benefit the most from side-blown smelting furnaces?
Industries such as steel production, non-ferrous metal processing, foundries, and recycling facilities benefit significantly from the efficiency and versatility of side-blown smelting furnaces.
5. What is the future outlook for side-blown smelting furnace technology?
The future of side-blown smelting furnace technology looks promising, with trends pointing towards increased automation, a focus on sustainability, and continuous R&D efforts to improve efficiency and reduce emissions.
Conclusion
In summary, side-blown smelting furnace equipment presents a multitude of advantages for various industrial applications. From enhanced efficiency and improved metal quality to reduced emissions and operational costs, these furnaces stand out as a superior choice in the metallurgical industry. As we move towards a more sustainable and efficient future, understanding the role of side-blown furnaces will be crucial for businesses aiming to remain competitive and environmentally conscious. Embracing this technology not only positions manufacturers for success but also aligns them with the broader goals of sustainability and resource efficiency in a rapidly changing industrial landscape.
TAG:
Previous:
Contact Us
Company Email:
962452762@qq.com
Contact Number:
+8615670922562
Company Address:
No. 11 Plant, Tiantan Industrial Park, Huling Industrial Cluster, Jiyuan City