Understanding the Importance of Lead Alloy Melting Equipment in Modern Manufacturing
Jul 16,2025
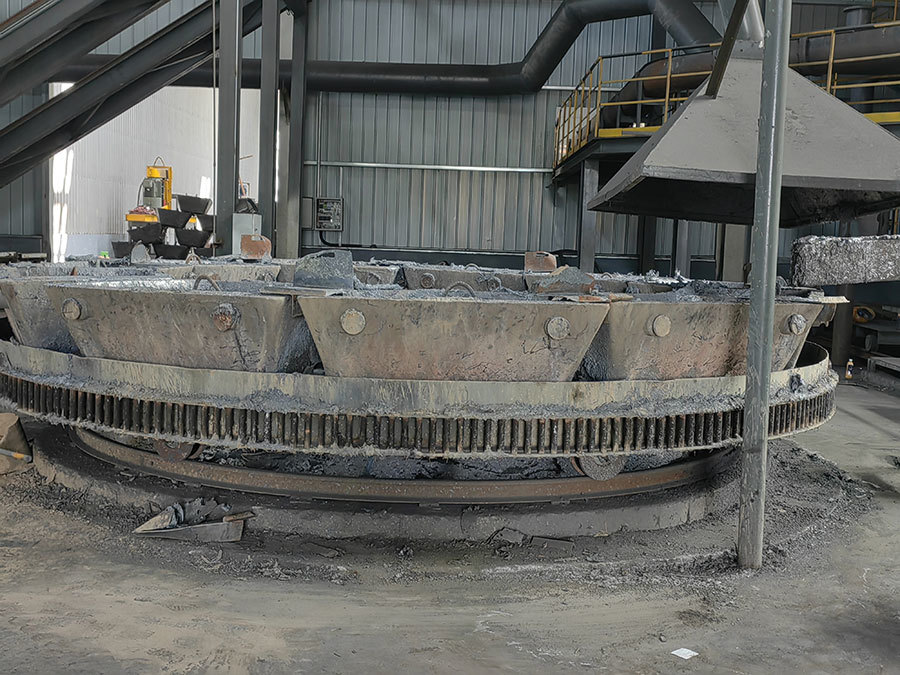
Understanding the Importance of Lead Alloy Melting Equipment in Modern Manufacturing
Table of Contents
- 1. Introduction to Lead Alloy Melting Equipment
- 2. The Importance of Lead Alloy Melting in Manufacturing
- 3. Key Applications of Lead Alloy Melting Equipment
- 4. Essential Components of Lead Alloy Melting Equipment
- 5. The Melting Process of Lead Alloys
- 6. Advantages of Modern Lead Alloy Melting Equipment
- 7. Sustainability and Lead Alloy Melting Equipment
- 8. Maintenance Tips for Lead Alloy Melting Equipment
- 9. Frequently Asked Questions
- 10. Conclusion
1. Introduction to Lead Alloy Melting Equipment
Lead alloy melting equipment plays a pivotal role in the manufacturing landscape. This specialized machinery is designed to melt lead alloys, which are crucial for various applications, including batteries, radiation shielding, and solder materials. Understanding the workings and importance of this equipment is essential for manufacturers aiming to optimize their production processes.
2. The Importance of Lead Alloy Melting in Manufacturing
The melting of lead alloys is not just a process; it is a cornerstone of modern manufacturing. The importance of this equipment can be highlighted through the following key points:
2.1 Enhancing Production Efficiency
Lead alloy melting equipment is engineered for high efficiency, ensuring that manufacturers can produce components rapidly without compromising quality. The advanced technology in these melting systems allows for precise temperature control, reducing the time it takes to melt and mold materials.
2.2 Ensuring Quality and Consistency
Quality assurance is essential in manufacturing, particularly for industries that require stringent standards. Lead alloy melting equipment guarantees uniform melting and consistent alloy compositions, which are critical for the performance of the final products.
3. Key Applications of Lead Alloy Melting Equipment
Lead alloys are utilized across a diverse range of industries. Some significant applications include:
3.1 Automotive Industry
In the automotive sector, lead alloys are commonly used in batteries, particularly lead-acid batteries, which remain a reliable choice for powering vehicles. The melting equipment ensures the production of high-quality battery components.
3.2 Electronics Manufacturing
Lead alloys serve as vital materials for soldering electronic components. The melting equipment allows manufacturers to produce solder with precise specifications, ensuring reliable electrical connections in electronic devices.
3.3 Construction and Infrastructure
Lead alloys are used in construction for radiation shielding and soundproofing materials. The melting equipment enables the efficient production of these components, contributing to safer and quieter environments.
4. Essential Components of Lead Alloy Melting Equipment
Understanding the components of lead alloy melting equipment is crucial for effective usage and maintenance. Key components include:
4.1 Melting Furnace
The melting furnace is the heart of the equipment, providing the necessary heat to melt the lead alloy. Different types of furnaces, such as induction and crucible furnaces, serve specific melting needs.
4.2 Temperature Control Systems
Accurate temperature control is vital for achieving desired melting results. Modern melting equipment incorporates advanced temperature control systems that allow for real-time monitoring and adjustments.
4.3 Pouring Systems
Once the alloy reaches the desired temperature, effective pouring systems ensure that the molten lead is transferred smoothly into molds without spillage or contamination.
5. The Melting Process of Lead Alloys
The melting process involves several critical steps:
5.1 Preparation of the Alloy
Before melting, the lead alloy needs to be prepared by sorting and cleaning the material to eliminate impurities that could affect quality.
5.2 Heating the Alloy
Using the melting furnace, the alloy is heated to its melting point. This stage requires precise temperature control to prevent overheating, which can degrade the metal's properties.
5.3 Pouring and Solidifying
Once melted, the alloy is poured into molds where it cools and solidifies. The efficiency of the pouring system plays a significant role in this process, impacting the final shape and quality of the product.
6. Advantages of Modern Lead Alloy Melting Equipment
Investing in modern lead alloy melting equipment can provide numerous advantages:
6.1 Increased Efficiency
With advancements in technology, modern systems significantly reduce melting times, resulting in quicker production cycles and improved overall efficiency.
6.2 Enhanced Safety Features
Safety is a primary concern in manufacturing settings. Modern melting equipment is equipped with safety features that minimize risks associated with high temperatures and molten metals.
6.3 Cost-Effectiveness
By optimizing melting processes and reducing waste, manufacturers can lower production costs, making modern equipment a financially sound investment.
7. Sustainability and Lead Alloy Melting Equipment
Sustainability is becoming increasingly important in manufacturing. Lead alloy melting equipment can contribute to more sustainable practices in several ways:
7.1 Recycling Lead Alloys
Modern melting equipment facilitates the recycling of lead alloys, reducing the need for new raw materials and minimizing environmental impact.
7.2 Energy Efficiency
Advanced technologies in melting equipment enable more energy-efficient operations, reducing overall energy consumption and the carbon footprint of manufacturing processes.
8. Maintenance Tips for Lead Alloy Melting Equipment
Proper maintenance of lead alloy melting equipment is essential for longevity and performance:
8.1 Regular Cleaning
Keeping the melting furnace and components clean prevents contamination and ensures optimal melting conditions.
8.2 Routine Inspections
Conducting regular inspections of temperature control systems and safety features can identify issues before they lead to significant problems.
8.3 Training for Operators
Ensuring that operators are well-trained in equipment usage and safety protocols is crucial for maintaining operational efficiency and preventing accidents.
9. Frequently Asked Questions
9.1 What types of lead alloys are commonly melted?
Commonly melted lead alloys include lead-tin, lead-calcium, and lead-antimony, each serving different applications.
9.2 How do I choose the right melting equipment?
Choosing the right equipment depends on the intended application, production volume, and specific melting requirements such as temperature control.
9.3 What safety precautions should be taken when using melting equipment?
Safety precautions include wearing protective gear, ensuring proper ventilation, and following manufacturer guidelines for equipment operation.
9.4 Can lead alloy melting equipment be used for recycling purposes?
Yes, modern melting equipment is designed to facilitate the recycling of lead alloys, making it a sustainable choice for manufacturers.
9.5 What maintenance is required for lead alloy melting equipment?
Regular cleaning, routine inspections, and operator training are essential maintenance practices that help ensure the equipment operates efficiently.
10. Conclusion
In conclusion, lead alloy melting equipment is an essential component of modern manufacturing processes. Its importance is evident in various applications across multiple industries, enhancing production efficiency, ensuring quality, and contributing to sustainable practices. By investing in advanced melting technology and adhering to proper maintenance protocols, manufacturers can significantly improve their operations and product outcomes. Understanding this equipment's intricacies allows us to fully appreciate its value in the manufacturing landscape of today.
TAG:
Previous:
Contact Us
Company Email:
962452762@qq.com
Contact Number:
+8615670922562
Company Address:
No. 11 Plant, Tiantan Industrial Park, Huling Industrial Cluster, Jiyuan City